The Pros and Cons of Preventive Maintenance for Businesses
Introduction
Preventive maintenance (PM) is a proactive approach to maintaining equipment and facilities by performing regular inspections, servicing, and repairs. Unlike reactive maintenance, which addresses issues after they arise, preventive maintenance aims to prevent problems before they occur. This strategy can lead to numerous benefits for businesses, but it also comes with its own set of challenges. Here’s an in-depth look at the pros and cons of preventive maintenance.
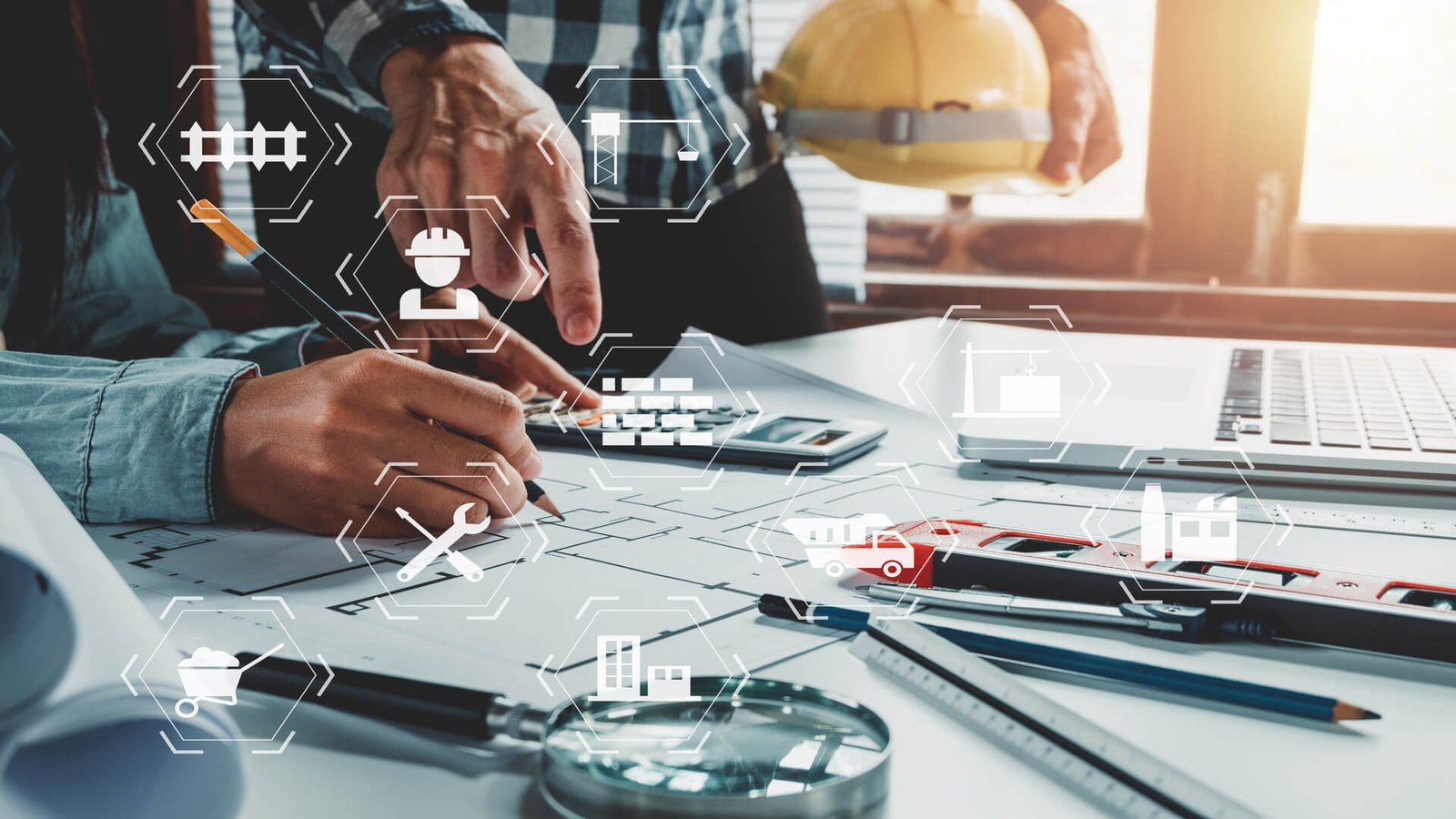
Pros of Preventive Maintenance
Increased Equipment Lifespan
One of the most significant advantages of preventive maintenance is its potential to extend the lifespan of equipment. By regularly inspecting and servicing machinery, businesses can identify and address issues before they lead to major failures. This proactive approach helps ensure that equipment remains in optimal condition for a longer period, thereby delaying the need for costly replacements.
Reduced Downtime
Unplanned downtime can be costly and disruptive for businesses. Preventive maintenance helps minimise unexpected breakdowns by addressing potential issues during scheduled maintenance windows. This proactive approach reduces the likelihood of sudden equipment failures, leading to smoother operations and less production downtime.
Cost Savings
While preventive maintenance involves initial costs for inspections and servicing, it can lead to significant long-term savings. By preventing major breakdowns and avoiding emergency repairs, businesses can reduce repair costs and the associated downtime. Moreover, maintaining equipment in good condition can lead to lower energy consumption and fewer production losses, further contributing to cost savings.
Improved Safety
Regular maintenance checks help identify and address safety hazards before they become serious problems. By ensuring that equipment operates safely and efficiently, businesses can create a safer working environment for employees. This proactive approach reduces the risk of accidents and injuries, contributing to overall workplace safety and compliance with health and safety regulations.
Enhanced Productivity
Well-maintained equipment operates more efficiently, leading to higher productivity levels. By minimising breakdowns and ensuring that machinery functions smoothly, businesses can achieve consistent production rates and meet deadlines more effectively. Enhanced productivity also contributes to improved customer satisfaction and a stronger competitive position in the market.
Cons of Preventive Maintenance
Initial Costs
Implementing a preventive maintenance program requires an initial investment in tools, training, and labour. Businesses must allocate resources for scheduled maintenance activities, which can be a significant financial commitment. For smaller businesses or those with limited budgets, these upfront costs can be a barrier to adopting preventive maintenance practices.
Resource Allocation
Preventive maintenance requires dedicated time and effort from staff. Regular inspections, servicing, and repairs can take time away from other critical tasks. This allocation of resources can be challenging for businesses with limited personnel or those operating in high-demand environments.
Over-Maintenance Risks
There is a risk of over-maintenance when a preventive maintenance program is not properly managed. Performing unnecessary maintenance activities or replacing parts that are still in good condition can lead to wasted resources and increased operational costs. It’s essential for businesses to strike the right balance between preventive maintenance and cost-efficiency.
Complexity in Planning
Developing and managing a preventive maintenance schedule can be complex, especially for businesses with diverse equipment and facilities. Creating an effective plan requires careful consideration of equipment usage patterns, maintenance intervals, and resource availability. This complexity can be a challenge for businesses without dedicated maintenance management expertise.
Potential for Inefficiencies
If not implemented correctly, preventive maintenance can lead to inefficiencies. For example, performing maintenance too frequently can disrupt operations and lead to unnecessary downtime. Additionally, if maintenance activities are not properly documented and tracked, businesses may struggle to assess the effectiveness of their preventive maintenance program.
What tools and technologies can assist in managing preventive maintenance activities?
Managing preventive maintenance activities efficiently requires leveraging a variety of tools and technologies designed to streamline processes, enhance accuracy, and improve overall effectiveness. One of the most valuable tools in this regard is Computerised Maintenance Management Systems (CMMS), which centralise maintenance data, schedule tasks, track inventory, and manage work orders. CMMS platforms like IBM Maximo, Maintenance Connection, and eMaint offer robust features such as automated reminders for scheduled maintenance, detailed reporting, and asset management. Additionally, Enterprise Asset Management (EAM) systems extend the capabilities of CMMS by integrating with other business processes, providing a comprehensive view of asset performance and lifecycle. For real-time monitoring, Internet of Things (IoT) sensors and predictive analytics tools can be employed to gather data on equipment conditions, predict potential failures, and optimise maintenance schedules based on actual performance metrics rather than fixed intervals. Mobile maintenance applications further enhance efficiency by allowing technicians to access maintenance schedules, update work orders, and document repairs directly from the field. Together, these tools and technologies facilitate a proactive maintenance strategy, reduce manual effort, and contribute to overall operational excellence.
What are the best practices for scheduling preventive maintenance tasks?
Scheduling preventive maintenance tasks effectively is crucial for maximising equipment uptime and minimising disruptions. One of the best practices is to establish a well-defined maintenance schedule based on the manufacturer’s recommendations, historical data, and equipment usage patterns. Regularly reviewing and updating the schedule ensures that it remains aligned with the operational needs and changes in equipment performance. Utilising a Computerised Maintenance Management System (CMMS) can significantly streamline scheduling by automating task reminders, tracking maintenance history, and integrating with other operational processes. It is also important to prioritise tasks based on criticality and impact, focusing on high-priority equipment that affects core operations. Balancing maintenance activities with production schedules helps to minimise downtime; scheduling maintenance during off-peak hours or planned production breaks can be particularly effective. Additionally, involving maintenance personnel in the scheduling process ensures that practical considerations and resource availability are accounted for. Regularly analysing the effectiveness of the maintenance schedule and making data-driven adjustments can further optimise performance and efficiency.